One can find plastic objects anywhere in their daily lives. Be it you, we, or anyone else. However, if you are curious to get into the manufacturing of the same, you can read this blog ahead. Today, we are sincerely explaining plastic forming processes. Some of them are quite common for industry experts. If you are planning to be one of them, this blog is for you.
Plastic Injection Molding

You can hold this method accountable for producing about 80 percent of the plastic stuff we use in our daily lives. The Injection Molding process actually makes full use of aluminum or steel molds.
The mold has two sides: core and cavity to be placed inside the PIM machine. This machine is held accountable for melting down the plastic pellets until they are molten. Next, these molten plastic particles are then injected into the cavity part of the mold, but that’s also under heated pressure.
The machine finally opens up when the plastic part is ready.
Its ability to make identical plastic parts in bulk makes it one of the most common plastic forming processes preferred by industrialists.
Molds are costly depending upon the part geometry. Careful engineer designs and measurements are still required to avoid any defect in bulk.
Extrusion Blow Molding
This process is useful to make inexpensive containers like disposable bottles, cups, can, or anything similar. These containers have thin walls. The process under the extrusion blow molding is easy and fast. But keep in mind not to make the part geometry complicated.
Also, it’s not the best manufacturing process when you need parts to have a high precision percentage.
Injection Blow Molding
Amongst other plastic forming processes available today, this process is best for using gas pressure to inject the molten resin into the cavity. This process can be controlled easily and repeated for bulk orders.
The best application of this method is for the manufacturing of transparent plastic water bottles. The process renders the product with excellent surface quality. But it would be equally poor for the items that would have thin walls.
PET or PEEK are usually the resins used for manufacturing transparent water bottles. These two resins are ideal because of their durability and clarity. Moreover, these resins help in making recyclable plastic water bottles.
Vacuum Casting
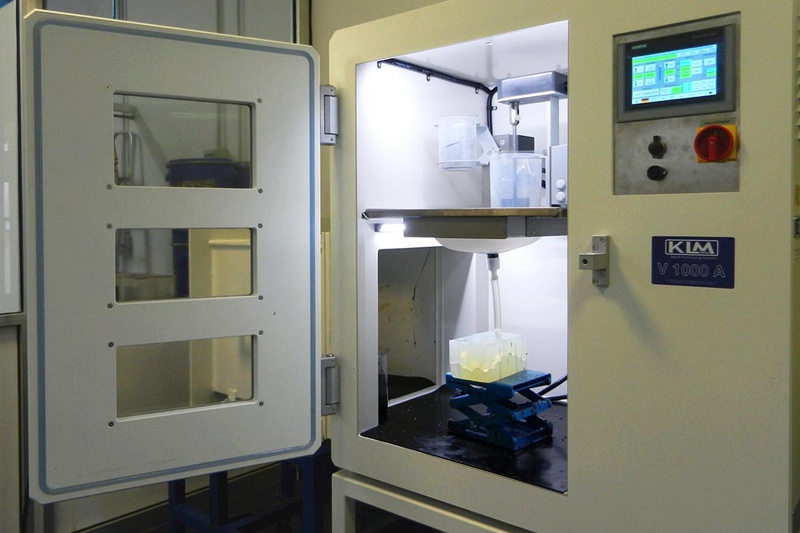
This process is chosen for the products to be produced in small numbers but with high quality. And you won’t need bigger investments or materials to manufacture rapid prototypes under this method.
You will choose a master model of a solid. Then place it into a sealed or enclosed box brimmed with flexible silicone or urethane. After that, you remove the master, leaving the scope for the formation of a cavity inside the mold.
Later on, you can inject resin inside this mold for making a prototype or a copy of the original product. Then, vacuum pressure is useful here to draw out any air bubbles, letting the resin settle inside the mold perfectly.
The mold is best to make 15-20 prototypes at a stretch. After that, the mold will degenerate.
Thermoforming
This is another form of vacuum forming. The expert engineer (which can also be you if you’re manufacturing the same) places a thick/thin gauge plastic sheet under the chosen die.
This die is hot and heated up to a certain temperature to make the material pliable. The pliable material or gauge sheet spreads over the die surface. Then, expert manufacturers use vacuum air pressure to draw out the sheet to finalize the material’s shape.
This process requires very basic equipment like a die, heating tools, and the material to heat over the surface. Its application is mostly for manufacturing cups, plastic clamshell packaging, lids, and boxes.
Rotational Molding
The rotational molding method also has the use of core and cavity. But it’s still slightly different.
Experts pour the plastic powder inside the mold cavity. They then place it in an oven. As the mold heats, it rotates on two axes. With gravity, the plastic starts to stick to the mold walls to form a better and thicker shape.
After that, we remove the mold from the oven and let it cool down. It might take about a few minutes, maybe around 15-20 minutes, for the mold to come back to room temperature.
Only after that, the part from the mold’s cavity is taken to another cycle.