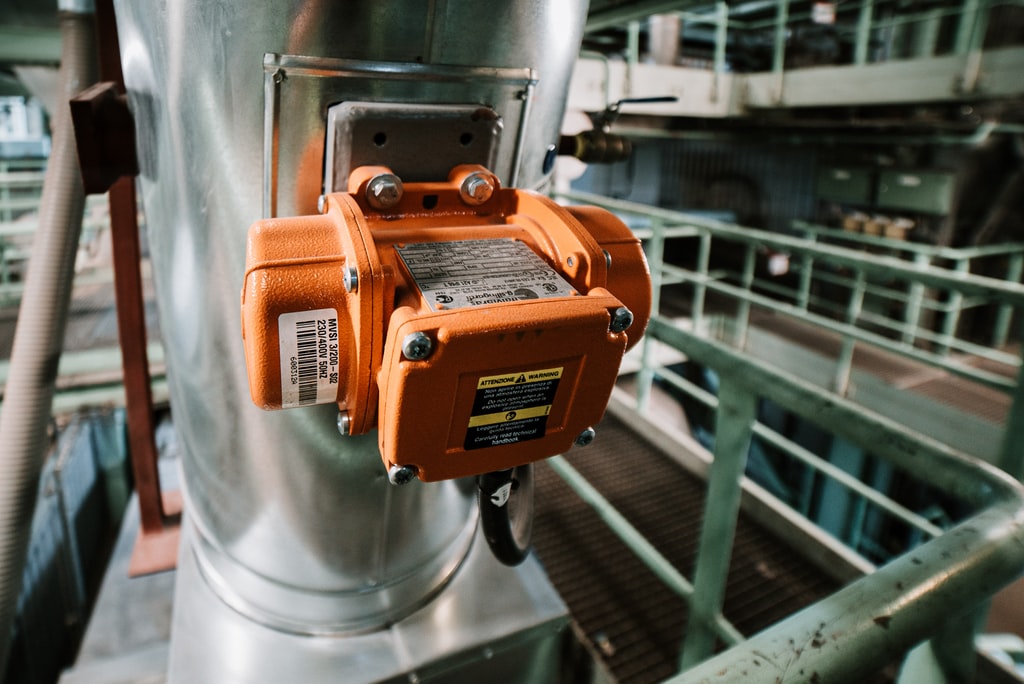
Industrial electric motors are vital to a company’s productivity and profitability. While operating these engines might seem simple and easy, their conditions and maintenance should never be neglected. Without proper care, some motors may end up in the trash pile prematurely, leading to a massive loss for your business. This is why it’s essential to provide your motor with a good running environment and regular preventive maintenance as part of caring for your facility assets. Here are some essential tips for maintaining an electric motor to ensure it’s running at its peak.
Conduct visual inspection
A quick visual check can help you discover essential details about your electric motor. Inspect its physical condition, and be sure to record your observations. If the motor runs in a rugged environment, you will likely notice corrosion or dirt buildup on its components.
Check the motor windings to detect any sign of overheating, such as a burnt smell. The relay and contacts should be free from dust and rust. Additionally, check the conditions of electric components, including your motor starters, and ensure they are tightly secured and free from dirt or grease. All these aspects may cause a potential internal issue since dirt may pose a risk to the efficiency of your motor, limiting its performance.Inspect the bearings regularly
Motor bearings are prone to wear and tear, so they will naturally cause problems from time to time. Ensure the motor is aligned correctly to prevent bearings from wearing out faster than they should. Misalignment can greatly strain one or both bearings.
Improper lubrication and dirt accumulation can also cause your bearings to wear out sooner than they should. Check your bearings for vibration and noise as they may indicate potential issues. If the bearing’s housing is too hot to touch, it might mean the motor is overheating or there is no adequate amount of grease.
The maintenance needs for bearing may vary, depending on the motor application and where the equipment is suited. There are some motors with low horsepower, and they never require lubrication since these have sealed bearings. You should be aware of the different types of bearings used in the plant and their repair needs.Check the rotor and stator
The stator and rotor are the heart of your electric motor. If one or both of these components are not working correctly, your motor will function poorly or even fail to run. Use a feeler gauge to measure the gap between the stator and rotor for equal diametrical clearance. Compare the readings to the manufacturer’s gap specifications. If there are differences, it is a clear sign of excessive wear in your bearings, and it might be time to replace them.Keep records
Take note every time you inspect your motor, replace bearings, adjust the belt tension, and add lubricant to your motors or bearings. This helps you better understand each part of the equipment, including problems addressed or replaced components. Your records will also be helpful for future audits and inspections.
Endnote
Proper maintenance will prolong your electric motor lifespan and prevent premature failures. It can detect potential issues and fix them before an enormous breakdown or delay in production. Ensure you follow the manufacturer’s recommendations for maintaining the equipment and lubricating the motor’s bearings to keep it running smoothly.